Precision at Your Fingertips: The Digital Torque Wrench
by admin
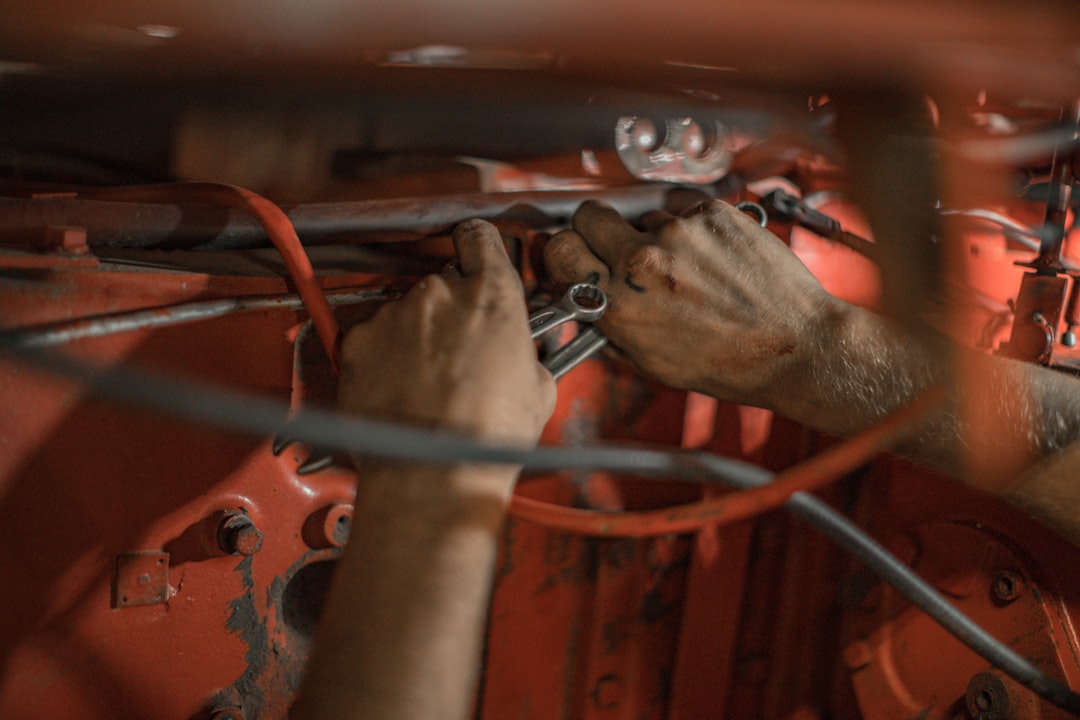
Digital torque wrenches are advanced tools used to measure and apply torque, or rotational force, to fasteners such as bolts and nuts. Unlike traditional torque wrenches, which rely on mechanical mechanisms to indicate the applied torque, digital torque wrenches use electronic sensors and displays to provide accurate and precise measurements. These tools have become increasingly popular in various industries due to their numerous benefits and advantages.
The history of torque wrenches dates back to the early 20th century when they were first developed for use in the automotive industry. As technology advanced, torque wrenches evolved from simple mechanical devices to more sophisticated digital tools. Today, digital torque wrenches are widely used in industries such as automotive, aerospace, manufacturing, construction, and maintenance and repair services.
The importance of torque wrenches in these industries cannot be overstated. Proper torque application is crucial for ensuring the integrity and safety of assembled components. Under-tightening can result in loose connections and potential failure, while over-tightening can lead to damage or even breakage of fasteners or components. Digital torque wrenches provide a reliable and accurate means of achieving the correct torque values, thereby reducing the risk of errors and accidents.
Key Takeaways
- Digital torque wrenches offer precise and accurate torque measurements for various applications.
- Benefits of using a digital torque wrench include increased efficiency, reduced errors, and improved safety.
- Digital torque wrenches work by measuring the rotational force applied to a fastener and converting it into a digital reading.
- Understanding torque measurement units such as Newton-meters and foot-pounds is crucial for using digital torque wrenches effectively.
- Types of digital torque wrenches include click, dial, and electronic torque wrenches, each with their own unique features and benefits.
Benefits of Using a Digital Torque Wrench
One of the main benefits of using a digital torque wrench is increased accuracy and precision. The electronic sensors in these tools provide real-time feedback on the applied torque, allowing for precise adjustments to be made. This ensures that the desired torque value is achieved consistently, resulting in reliable and secure fastenings.
Digital torque wrenches also offer time-saving features that can greatly improve efficiency in various applications. These tools often have preset torque values that can be easily selected, eliminating the need for manual calculations or adjustments. Additionally, some digital torque wrenches have built-in memory functions that can store multiple torque values, further streamlining the process.
Ease of use is another advantage of digital torque wrenches. The electronic displays provide clear and easy-to-read readings, making it simple for users to monitor and adjust the applied torque. Many digital torque wrenches also have user-friendly interfaces and intuitive controls, making them accessible to both experienced professionals and beginners.
Using a digital torque wrench can also reduce the risk of errors and accidents. The real-time feedback provided by these tools helps prevent over-tightening or under-tightening, which can lead to costly mistakes or safety hazards. Additionally, some digital torque wrenches have built-in warning systems that alert users when the desired torque value is reached, further ensuring accuracy and preventing damage.
Cost-effectiveness is another significant benefit of digital torque wrenches. While these tools may have a higher upfront cost compared to traditional torque wrenches, their accuracy and reliability can save money in the long run. By preventing over-tightening or under-tightening, digital torque wrenches help avoid costly repairs or replacements due to damaged fasteners or components.
How a Digital Torque Wrench Works
Digital torque wrenches consist of several key components that work together to measure and apply torque accurately. These components include a handle or grip, a torque sensor, an electronic display, and various control buttons or settings.
The torque sensor is the heart of a digital torque wrench. It measures the rotational force applied to the fastener and converts it into an electrical signal. This signal is then processed by the internal electronics of the tool and displayed on the electronic display.
Operating principles of digital torque wrenches vary depending on the type of sensor used. Some digital torque wrenches use strain gauge sensors, which measure the deformation of a metal element under applied torque. Others use magnetic sensors, which detect changes in magnetic fields caused by the applied force. Regardless of the sensor type, the principle remains the same: converting mechanical force into an electrical signal for measurement and display.
In comparison to traditional torque wrenches, digital torque wrenches offer several advantages. Traditional torque wrenches rely on mechanical mechanisms such as springs or clickers to indicate the applied torque. While these tools can be accurate, they are often less precise and require manual interpretation of the torque value. Digital torque wrenches, on the other hand, provide real-time digital readings, eliminating the need for guesswork or estimation.
Understanding Torque Measurement Units
To fully understand digital torque wrenches, it is important to have a basic understanding of torque and its measurement units. Torque is a rotational force that causes an object to rotate around an axis. It is commonly measured in units such as Newton meters (Nm), foot-pounds (ft-lb), inch-pounds (in-lb), and kilogram-force meters (kgf-m).
Newton meters (Nm) is the most widely used unit for measuring torque. It represents the amount of force required to rotate an object one meter from its axis of rotation. Foot-pounds (ft-lb) and inch-pounds (in-lb) are commonly used in the United States and represent the amount of force required to rotate an object one foot or one inch from its axis of rotation, respectively. Kilogram-force meters (kgf-m) are used in some countries and represent the amount of force required to rotate an object one meter from its axis of rotation under the influence of gravity.
Conversion between torque units can be done using conversion factors. For example, 1 Nm is approximately equal to 0.7376 ft-lb, 8.8507 in-lb, or 0.10197 kgf-m. These conversion factors can be useful when working with torque specifications or when comparing different torque measurement units.
Types of Digital Torque Wrenches
Digital torque wrenches come in various types, each designed for specific applications and requirements. The main types of digital torque wrenches include electronic torque wrenches, click-type torque wrenches, dial-type torque wrenches, angle torque wrenches, and multi-functional torque wrenches.
Electronic torque wrenches are the most advanced type of digital torque wrenches. They feature a digital display that provides real-time torque readings and often have additional features such as memory functions and data logging capabilities. Electronic torque wrenches are commonly used in industries where precise torque control is critical, such as aerospace and automotive manufacturing.
Click-type torque wrenches are a popular choice for general-purpose applications. They have a click mechanism that produces an audible or tactile signal when the desired torque value is reached. Click-type torque wrenches are easy to use and provide reliable torque control, making them suitable for a wide range of industries and applications.
Dial-type torque wrenches have a dial or gauge that displays the applied torque. They are often used in applications where a visual indication of the torque value is required. Dial-type torque wrenches are commonly used in maintenance and repair services, as well as in industries where frequent adjustments to torque values are necessary.
Angle torque wrenches measure the angle of rotation in addition to the applied torque. They are used in applications where the angle of rotation is critical, such as tightening bolts with specific angular requirements. Angle torque wrenches are commonly used in the automotive industry, particularly for engine assembly and other precision applications.
Multi-functional torque wrenches combine multiple functions into a single tool. These tools often have interchangeable heads or attachments that allow for different types of fasteners to be tightened or loosened. Multi-functional torque wrenches are versatile and can be used in various industries and applications where different types of fasteners are encountered.
Choosing the Right Digital Torque Wrench for Your Needs
When selecting a digital torque wrench, there are several factors to consider to ensure that you choose the right tool for your needs. These factors include the torque range, accuracy, size and weight, ergonomics, and budget.
The torque range of a digital torque wrench refers to the minimum and maximum torque values that the tool can measure or apply. It is important to choose a torque wrench with a range that matches the torque requirements of your application. If the torque range is too narrow, you may not be able to achieve the desired torque value. On the other hand, if the torque range is too wide, the tool may not provide accurate readings at lower torque values.
Accuracy is another crucial factor to consider when selecting a digital torque wrench. The accuracy of a torque wrench is typically expressed as a percentage of the applied torque value. For example, a torque wrench with an accuracy of ±3% means that the actual torque value can deviate by up to 3% from the displayed value. It is important to choose a torque wrench with sufficient accuracy for your application to ensure reliable and precise torque control.
The size and weight of a digital torque wrench can also impact its usability and comfort during use. A compact and lightweight tool may be more suitable for applications that require frequent or prolonged use. However, it is important to strike a balance between size and weight and the required torque range and accuracy. Choosing a tool that is too small or light may sacrifice performance or durability.
Ergonomics is another important consideration when selecting a digital torque wrench. The handle or grip should be comfortable to hold and provide a secure grip to prevent slippage during use. Some digital torque wrenches have ergonomic designs or features such as rubberized grips or anti-slip coatings to enhance user comfort and safety.
Budget considerations are also important when choosing a digital torque wrench. While it may be tempting to opt for the cheapest option available, it is important to consider the quality and reliability of the tool. Investing in a high-quality digital torque wrench from a reputable manufacturer may result in better performance, accuracy, and durability, ultimately saving money in the long run.
Calibration and Maintenance of Digital Torque Wrenches
Regular calibration and maintenance are essential for ensuring the accuracy and reliability of digital torque wrenches. Calibration is the process of comparing the displayed torque value of a torque wrench with a known reference value to determine its accuracy. It is recommended to calibrate digital torque wrenches at regular intervals, typically every 6 to 12 months, or as specified by the manufacturer.
Calibration procedures for digital torque wrenches may vary depending on the manufacturer and model. However, they generally involve applying a known torque value to the wrench and comparing the displayed value with the reference value. If there is a significant deviation, adjustments may need to be made to bring the tool back into calibration.
Maintenance tips for prolonging the lifespan of digital torque wrenches include keeping them clean and free from debris or contaminants, storing them in a dry and secure location, and avoiding excessive force or impact. It is also important to follow any specific maintenance instructions provided by the manufacturer.
Common Applications of Digital Torque Wrenches
Digital torque wrenches find applications in various industries where precise torque control is critical. Some common applications include:
– Automotive industry: Digital torque wrenches are widely used in automotive manufacturing and repair services for tightening bolts and nuts to specific torque values. They are essential for ensuring the safety and reliability of automotive components.
– Aerospace industry: The aerospace industry requires precise torque control for assembling aircraft components. Digital torque wrenches are used in engine assembly, wing assembly, and other critical applications where accurate torque values are crucial.
– Manufacturing industry: Digital torque wrenches are used in various manufacturing processes where fasteners need to be tightened or loosened with precise torque control. They are commonly used in industries such as electronics, appliances, machinery, and furniture manufacturing.
– Construction industry: Digital torque wrenches are used in construction applications where fasteners need to be tightened to specific torque values. They are commonly used in structural steel assembly, concrete formwork, and other construction projects.
– Maintenance and repair services: Digital torque wrenches are essential tools for maintenance and repair services where fasteners need to be tightened or loosened with precise torque control. They are commonly used in industries such as automotive repair, machinery maintenance, and equipment servicing.
Safety Tips for Using Digital Torque Wrenches
Using digital torque wrenches safely is crucial to prevent accidents or damage. Here are some safety tips to keep in mind:
– Proper handling and storage of torque wrenches: Always handle torque wrenches with care and avoid dropping or mishandling them. Store them in a secure location away from moisture or extreme temperatures.
– Personal protective equipment: Wear appropriate personal protective equipment such as safety glasses, gloves, and ear protection when using digital torque wrenches, especially in noisy or hazardous environments.
– Precautions when working with high torque values: When working with high torque values, ensure that the tool is properly calibrated and capable of handling the required torque. Use appropriate techniques and leverage to avoid strain or injury.
– Avoiding over-tightening or under-tightening: Follow the specified torque values for your application and avoid over-tightening or under-tightening fasteners. Use the digital display on the torque wrench to monitor the applied torque and make adjustments as necessary.
Future Developments in Digital Torque Wrench Technology
The future of digital torque wrench technology holds exciting possibilities for further advancements. Some potential developments include:
– Advancements in sensor technology: As sensor technology continues to improve, digital torque wrenches may become even more accurate and precise. New sensor materials and designs may allow for higher torque ranges and better performance in various applications.
– Integration with smart devices and software: Digital torque wrenches may become integrated with smart devices and software, allowing for wireless connectivity and remote monitoring. This could enable real-time data logging, analysis, and reporting, enhancing productivity and efficiency.
– Wireless connectivity and remote monitoring: Wireless connectivity may allow digital torque wrenches to communicate with other devices or systems, such as computers or control panels. This could enable seamless integration into automated assembly lines or quality control processes.
– Improved durability and reliability: Future developments may focus on improving the durability and reliability of digital torque wrenches. This could involve the use of more robust materials, enhanced sealing against dust and moisture, and improved battery life.
In conclusion, digital torque wrenches have revolutionized the way torque is measured and applied in various industries. These advanced tools offer increased accuracy, time-saving features, ease of use, reduced risk of errors and accidents, and cost-effectiveness. Understanding how digital torque wrenches work, the different types available, and how to choose the right tool for your needs is crucial for achieving reliable and precise torque control. Regular calibration and maintenance are essential for ensuring the accuracy and reliability of digital torque wrenches. By following safety tips and staying informed about future developments in digital torque wrench technology, users can maximize the benefits of these tools in their respective industries.
Looking for more information on digital torque wrenches? Check out this insightful article on the benefits of using digital torque wrenches in various industries. From improving accuracy and efficiency to reducing human error, digital torque wrenches have revolutionized the way torque is measured and applied. To learn more about this innovative tool, click here: https://www.ahamorphous.com/.
FAQs
What is a digital torque wrench?
A digital torque wrench is a tool used to apply a specific amount of torque to a fastener, such as a bolt or nut, with the help of digital technology.
How does a digital torque wrench work?
A digital torque wrench works by using a strain gauge to measure the amount of force applied to the fastener. The tool then converts this force into a digital reading that is displayed on a screen.
What are the advantages of using a digital torque wrench?
The advantages of using a digital torque wrench include increased accuracy, ease of use, and the ability to store and recall torque settings.
What types of digital torque wrenches are available?
There are several types of digital torque wrenches available, including click-type, dial-type, and electronic torque wrenches.
What is the accuracy of a digital torque wrench?
The accuracy of a digital torque wrench can vary depending on the model and manufacturer, but most digital torque wrenches have an accuracy of +/- 2% or better.
What is the range of torque that a digital torque wrench can measure?
The range of torque that a digital torque wrench can measure can vary depending on the model and manufacturer, but most digital torque wrenches have a range of 10-1000 Nm.
Can a digital torque wrench be calibrated?
Yes, a digital torque wrench can be calibrated to ensure that it is measuring torque accurately. Calibration should be done regularly to maintain the accuracy of the tool.
Digital torque wrenches are advanced tools used to measure and apply torque, or rotational force, to fasteners such as bolts and nuts. Unlike traditional torque wrenches, which rely on mechanical mechanisms to indicate the applied torque, digital torque wrenches use electronic sensors and displays to provide accurate and precise measurements. These tools have become increasingly…